Processes
Depending on the design parameters required by your project, certain casting processes are more cost efficient. The 3 most common casting processes are, sand casting, centrifugal casting, and continuous casting.
Continuous Casting
The continuous cast process grants the ability to create near net, rounds, rectangles, or hollow tubes up to 144" in length. No matter how large or small the quantity we keep an inventory of stock sizes to cut to your desired length. The continuous process saves times, energy, and labor by using a cooled mold to promote continuous solidification.
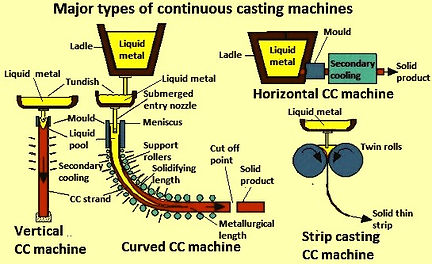
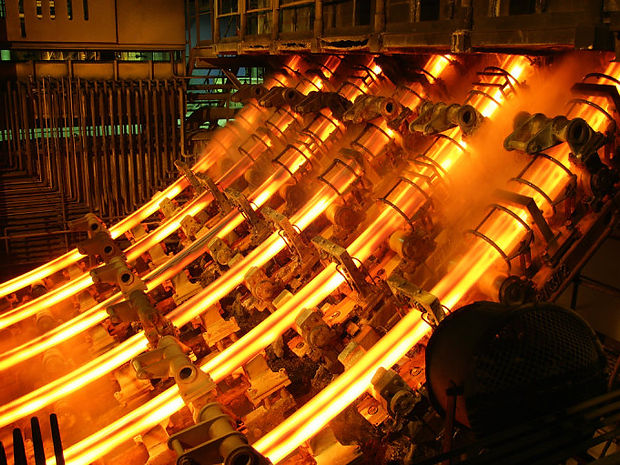
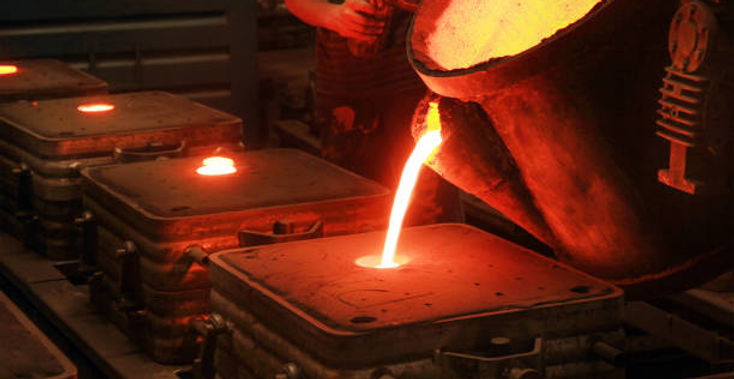
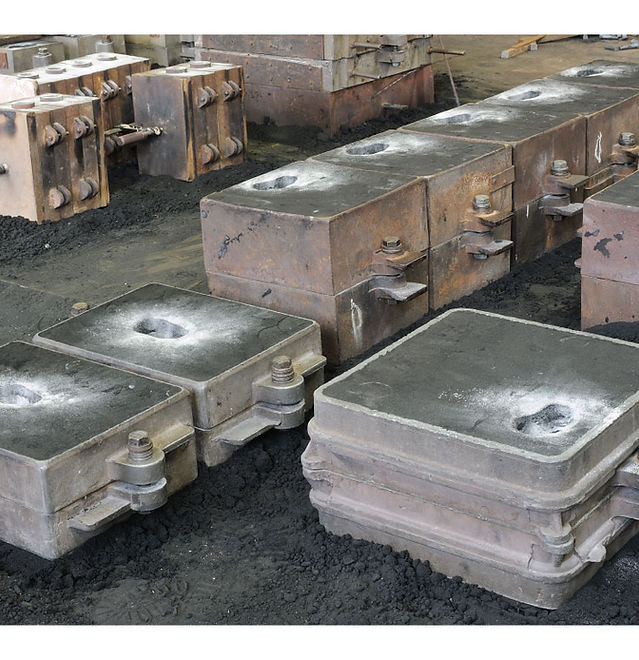
Sand Casting
Sand Casting is a process that goes back as far as ancient Egypt. Molds are prepped using either sand or silica in a mold comprised of a cope and a drag. A wood, plastic, or foam pattern is used to create a cavity to produce the desired part shape. Molten metal is then poured into the mold through a sprue to runners and gates and into the cavity. The metal then solidifies and is removed from the mold and cleaned. These products can be shipped directly in the as cast condition or machined further.

Centrifugal Castings
Centrifugal casting uses a mold that is fixed to a spinning element. This process lends itself to part configurations such as tubes. Due to the centrifugal forces the molten material is subject to, it allows for directional solidification which decreases the likelihood of defects being present in the final part. Centrifugal casting processing is not well suited for solid or square configurations.
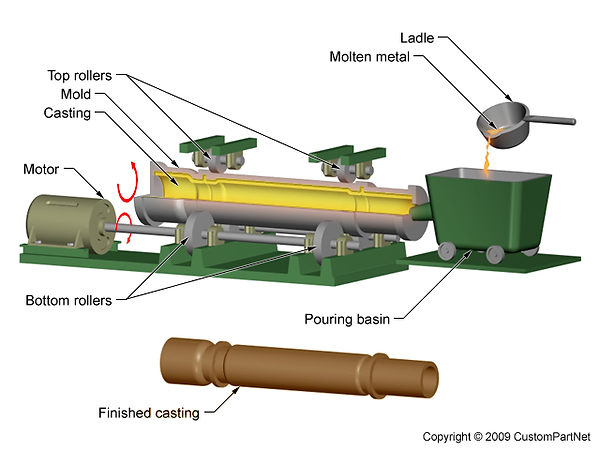

Finished Parts
Endit metals proudly offers a wide array of subtractive manufacturing. Both manual and CNC machine centers are utilized to produce your project needs. We offer engineering services and/or can work from you or your customers prints. Our experienced machinists are capable of handling all of your technical needs.
​
​
​
​
​
​
​
Request a quote today!!